Explore the wide-ranging uses of sheet metal fabrication in various industries, from automotive and construction to home appliances and aerospace.
Learn how sheet metal is transformed into essential components like car bodies, ductwork, roofing panels, and custom enclosures through cutting, bending, and assembling processes.
Discover how this versatile fabrication method supports both functional and decorative applications, providing strength, precision, and adaptability for diverse manufacturing and architectural needs.
What is sheet metal fabrication?
Sheet metal fabrication is the process of transforming flat sheets of metal into specific shapes or structures. It involves various techniques such as cutting, bending, and assembling to create metal parts, products, or prototypes. Common materials used in sheet metal fabrication include stainless steel, aluminium, copper, and cold-rolled steel.
Each metal sheet is chosen based on factors like strength, corrosion resistance, and ease of fabrication. The process starts with raw metal sheets and, through various methods, results in the final product. This manufacturing process is crucial in many industries, offering high-quality and durable metal parts suitable for a wide range of applications.
What is sheet metal used for?
Sheet metal fabrication is used in numerous industries due to its versatility and durability.
In aerospace, sheet metal is crucial for creating high-strength, lightweight components for aircraft, where precision and accuracy are essential for safety and performance. It is also used in the automotive industry. Sheet metal parts are essential for producing car body panels, chassis, and other vehicle components. It helps manufacture durable and corrosion-resistant products.
For construction, sheet metal fabrication is ideal for forming structural elements, such as roofing, cladding, and frameworks. Common materials like zinc and stainless steel are favoured due to their strength and corrosion resistance. Aluminium is often used because of its lightweight properties and durability. These materials ensure long-lasting, reliable structures suitable for varying types of construction projects.
The healthcare industry requires high-quality and sterile equipment. Sheet metal is used to manufacture medical devices, hospital furniture, and equipment, ensuring they meet strict hygiene standards. These items include surgical tables, diagnostic machines, and storage units, all designed to maintain sterility and support patient care.
When producing household appliances, sheet metal is used to create durable and robust products. These include ovens, refrigerators, and washing machines. Different types of sheet metal allow for various designs and functionalities.
Stainless steel, for example, is popular for its corrosion resistance, while galvanised steel offers added protection against rust, ensuring long-lasting performance and reliability.
These are just a few examples of how sheet metal fabrication is a crucial part of manufacturing and assembling a wide range of products across different sectors.
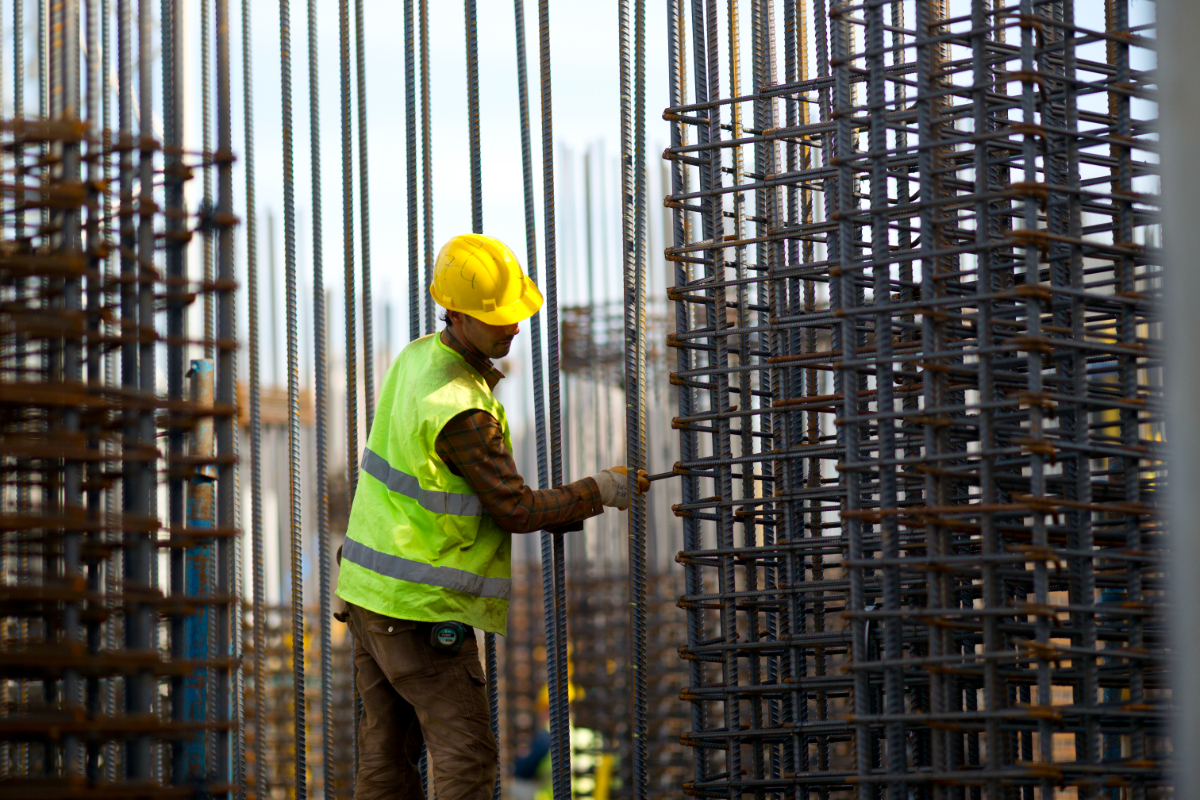
Methods of cutting sheet metal
Cutting sheet metal involves several techniques, each chosen based on the material, thickness, and intended final product.
Laser Cutters: Laser cutting uses a laser beam to make precise cuts in the metal. It offers high accuracy and is suitable for complex shapes and small holes. This method is efficient and can handle a variety of materials beyond metal, such as wood and acrylic. Ideal for detailed and intricate designs.
Plasma Cutting: Plasma cutting utilises a high-pressure stream of ionised gas to melt and cut metal efficiently. It's faster than laser cutters and can handle thicker materials with ease. This method is cost-effective and often used in various industries for precise and rapid metal-cutting tasks.
Shearing: Shearing involves cutting metal sheets using a shear machine. This method is commonly used for straight cuts and can handle different sizes and thicknesses. It's efficient and typically produces clean edges with minimal waste. Shearing is widely utilised in various industries, including automotive, construction, and manufacturing.
CNC Machining: CNC (Computer Numerical Control) machining uses automated machinery to cut metal sheets with high precision. This technique is ideal for mass production and complex designs. It ensures consistent quality, reducing human error. CNC machining is used on various materials, including metals, plastics, and composites, offering flexibility in manufacturing.
Each method has its advantages, and the choice depends on factors like material type, desired precision, and production scale.
What tools do you need for sheet metal fabrication?
Sheet metal fabrication requires a variety of tools and machinery to ensure precise and accurate results.
Bending Machines: Press brakes are commonly used in bending machines. They apply pressure to bend metal sheets into specific shapes and angles.
Cutting Tools: Cutting tools like laser cutters, plasma cutters, and shearing machines are essential for making precise cuts in sheet metal.
Welding Equipment: Different types of welding equipment, such as MIG (Metal Inert Gas) and spot welding machines, are used for joining metal parts.
Punching Machines: Punching machines, such as CNC punching, create holes in metal sheets. They are vital for producing prototypes and final products with complex designs.
Riveting Tools: Riveting tools join metal pieces together without welding, ensuring strong and durable connections.
Having the right tools and machinery is crucial for any sheet metal fabrication project, ensuring high-quality and accurate metal products.

What is sheet metal bending?
Sheet metal bending is a fabrication process that involves shaping metal sheets by applying force. The process is crucial in forming metal parts and products used in various applications.
Three common techniques for Bending:
Press Brake Bending: This method uses a press brake to apply pressure, bending the metal sheet into the desired shape. It ensures precision and is suitable for a wide range of metal sheets. The process is highly efficient and can handle various thicknesses, making it ideal for both small and large-scale projects. Skilled operators ensure each bend is accurate and consistent.
Roll Bending: Roll bending involves passing the metal sheet through a series of rollers to gradually shape it into a curve or cylinder. This technique is ideal for creating large bends and rounded shapes. It is used in industries where precision and smooth curves are essential, such as in the manufacturing of pipes, tanks, and complex structural components.
Air Bending: In air bending, the metal sheet is bent by pressing it against a die. This method offers flexibility in creating different angles and shapes. It’s a popular technique due to its efficiency and precision, allowing for the manufacture of complex parts. By adjusting the position of the die and punch, a variety of bends can be achieved effectively.
Bending offers several advantages. It provides flexibility, allowing the creation of various shapes and designs. It also maintains the material's high strength without causing damage. Bending is cost-effective, as it reduces the need for welding and lowers production costs.
When bending sheet metal, it is important to consider the type of material, its thickness, and the desired shape. Using the right technique and machinery ensures precision and quality in the final product.
Sheet metal bending is an essential step in the sheet metal fabrication process, offering a way to produce high-strength, durable, and complex metal parts.
For further details about sheet metal fabrication services or to discuss your project, please contact local specialists in your area. Many will work with you closely to understand and provide your requirements.